R&G Wiki Grundlagenwissen
Warum Faserverbundwerkstoffe?
(Quelle: DLR Stuttgart)
Weitere Werkstoffvorteile
- Geringe Wärmeausdehnung
- Korrosionsbeständigkeit
- Stufenweises Versagen
- Hohe Schwingfestigkeit
- Günstiges Schlagverhalten
Kostengünstige Bauweisen
- Weniger Einzelteile
- Geringer Materialabfall
- Gute Formbarkeit
Was sind Faserverbundwerkstoffe?
Verschiedenartige Materialien zu einem Werkstoffverbund zu kombinieren, um verbesserte Eigenschaften zu erzielen, ist in der Natur ein ebenso selbstverständliches Prinzip wie der Leichtbau. Diese, der Natur abgeschaute Bauweise hat viele technische Bereiche geradezu revolutioniert. Erstmals stehen hochfeste und dabei leichte Werkstoffe mit überragenden Eigenschaften zur Verfügung. Insbesondere in der Luft- und Raumfahrt werden durch niedrige Strukturgewichte wesentliche Energieeinsparungen und Leistungssteigerungen erzielt.
Der Einsatz von Hochleistungs-Faserverbundwerkstoffen in der Raumfahrt ist vor allem wirtschaftlich begründet. Wegen der hohen Energiekosten ist man bereit, in diesem Bereich bis zu € 25.000 pro kg Gewichtsersparnis aufzuwenden. Bei der Luftfahrtindustrie sind dieses 250 - 750 €/kg, in der Fahrzeugindustrie 0 - 2,50 €/kg (ausgenommen im Rennsport).
Da FVW im allgemeinen teurer sind als Kompaktwerkstoffe (z.B. Metalle) und höhere Anforderungen an die Auslegung und die Verarbeitungstechnologie gestellt werden, ist dieser Anreiz für den normalen Fahrzeugbau relativ gering, während er in der Luft- und Raumfahrt deutlich zum Tragen kommt.
Mit sinkendem Preis und zunehmendem, allgemein zugänglichem Know-How für die Verarbeitung haben sich FVW auf breiter Ebene durchgesetzt. Kaum noch wegzudenken sind sie im Motorsport, Modell- und Sportgerätebau. Anwendungen im Maschinenbau sind im Vormarsch.
(Quelle: DLR Stuttgart)
Weitere Infos Faserverbundwerkstoffe
Konstruieren mit Faserverbundwerkstoffen
Faserverbundwerkstoffe sind anders als Metalle
- Richtungsabhängige Eigenschaften
- Werkstoffendzustand wird erst im Bauteil erreicht
- Vielfältige Gestaltungsmöglichkeiten durch Variation von:
a.) Faser- und Matrixwerkstoff
b.) Faserrichtung
c.) Lagenanzahl
(Quelle: DLR Stuttgart)
Regeln der Bauteilgestaltung
- Fasern in Richtung der angreifenden Lasten
- Möglichst symmetrischer Lagenaufbau
- Großflächige Krafteinleitungen
Kennwerte von Duroplasten
Werkstoff |
Dichte |
Bruchdehnung | Lieferform | Verarbeitungstemperatur | Gebrauchstemperatur der Bauteile |
---|---|---|---|---|---|
UP ungesättigte Polyesterharze | 1,12 - 1,25 g/cm³ | > 3 % | flüssig | Raumtemperatur bis 180°C |
50 - 160 °C |
EP Epoxidharze |
1,1 - 1,25 g/cm³ | 6 - 8 % | flüssig | Raumtemperatur bis 230°C | 45 - 230 °C |
Die Bruchdehnung von Laminierharzen sollte vorzugsweise gleich oder grös-ser der Bruchdehnung der Verstärkungsfasern sein, damit im Belastungsfall kein Bauteilversagen durch Brüche und Risse im Harz eintritt.
Verarbeitungstemperatur:
Der höchste Wert beschreibt die maximal erforderliche Temperatur bei der Warmhärtung. Diese Warmhärtung ist nur bei einigen Temperharzen mit entsprechend hoher Temperaturbelastbarkeit erforderlich.
Die überwiegend angebotenen kalthärtenden Harze erreichen bei Raumtemperatur nahezu ihre volle Festigkeit. Die Gebrauchstemperatur der Bauteile liegt meist bei 50-80 °C.
Werkstoff |
Verarbeitungsschwindung |
Nachschwindung | Reaktionswärme | Lagerfähigkeit |
---|---|---|---|---|
UP ungesättigte Polyesterharze | -10, linear um 2 % | bis 3 % |
exotherme Reaktion mit teilweise hoher Wärmeentwicklung (besonders beim Vergießen zu berücksichtigen, Härter entsprechend auswählen). |
dunkel, kühl, gut verschlossen bis 6 Monate |
EP Epoxidharze | 1 - 3 % | < 1 % |
dunkel, kühl, gut verschlossen |
Verarbeitungsschwindung
Der Schwund erfolgt bei Epoxidharzen in der flüssigen Phase, also hauptsächlich innerhalb der Verarbeitungszeit.
Die Nachschwindung ist bei unverstärkten Harzmassen am größten. Verstärkungen, z.B. durch Glasgewebeeinlagen, verringern das Schwundmaß erheblich. Beim Tempern (Nachhärten bei erhöhter Temperatur)
ist ebenfalls eine leichte Nachschwindung zu erwarten, da sich noch reaktionsfähige Harz- und Härtermoleküle verbinden und somit enger zusammentreten.
Werkstoff |
Beständig gegen |
Nicht beständig gegen (eine Auswahl) |
Brennbarkeit | Reparatur |
---|---|---|---|---|
UP ungesättigte Polyesterharze |
Wasser, wäßrige Lösungen, Heizöl, Benzin |
heißes Wasser, konzentrierte Säuren und Laugen, Benzol, Alkohol, Toluol | nicht selbstverlöschend | auflaminieren und kleben |
EP Epoxidharze | Alkohol, Benzin, Benzol, Mineralöle, Fette | heißes Wasser, Ester, konzentrierte Säuren und Laugen, Ketone, Aceton |
schwer entzündbar, |
Werkstoff |
Zugfestigkeit MPa |
Zugmodul GPa | Biegefestigkeit MPa | Biegemodul GPa |
---|---|---|---|---|
UP ungesättigte Polyesterharze |
50 - 70 | 3,5 - 4,7 | 60 - 120 | 4,0 - 5,0 |
EP Epoxidharze |
70 - 90 | 2,8 - 3,6 | 140 - 160 | 4,5 - 6,0 |
Verschiedenartige Materialien zu einem Werkstoffverbund zu kombinieren, um verbesserte Eigenschaften zu erzielen, ist in der Natur ein ebenso selbstverständliches Prinzip wie der Leichtbau.
Diese, der Natur abgeschaute Bauweise hat viele technische Bereiche geradezu revolutioniert. Erstmals stehen hochfeste und dabei leichte Werkstoffe mit überragenden Eigenschaften zur Verfügung.
Insbesondere in der Luft- und Raumfahrt werden durch niedrige Strukturgewichte wesentliche Energieeinsparungen und Leistungssteigerungen erzielt.
Der Einsatz von Hochleistungs-Faserverbundwerkstoffen in der Raumfahrt ist vor allem wirtschaftlich begründet. Wegen der hohen Energiekosten ist man bereit, in diesem Bereich bis zu Euro 25.000 pro kg Gewichtsersparnis aufzuwenden. Bei der Luftfahrtindustrie sind dieses 250 - 750 Euro/kg, in der Fahrzeugindustrie 0 - 2,50 Euro/kg (ausgenommen im Rennsport).
Da FVW im allgemeinen teurer sind als Kompaktwerkstoffe (z.B. Metalle) und höhere Anforderungen an die Auslegung und die Verarbeitungstechnologie gestellt werden, ist dieser Anreiz für den normalen Fahrzeugbau relativ gering, während er in der Luft- und Raumfahrt deutlich zum Tragen kommt.
Mit sinkendem Preis und zunehmendem, allgemein zugänglichem Know-How für die Verarbeitung haben sich FVW auf breiter Ebene durchgesetzt. Kaum noch wegzudenken sind sie im Motorsport, Modell- und Sportgerätebau. Anwendungen im Maschinenbau sind im Vormarsch.
Das Funktionsprinzip
Ein Faserverbundwerkstoff (FVW) wird durch Zusammenfügen mehrerer Werkstoffe hergestellt:
- der formgebenden Matrix (z.B. Epoxid- oder Polyesterharz)
- den verstärkenden, hochfestenFasern (meist Glas-, Aramid- und Kohlenstoff)
Hauptsächlich benötigte Werkstoffe: ein Harzsystem und Verstärkungsfasern
Faserverbundwerkstoffe sind im Prinzip vergleichbar mit Stahlbeton, bei dem ein spröder, formgebender Werkstoff (Beton) durch Stahleinlagen verstärkt wird.
Die Fasern werden in eine flüssige Reaktionsharzmasse eingebettet und beim Härten des Harzes in dem so entstehenden festen Formstoff verankert. Auch kompliziert gestaltete und sehr große Teile können in einem Arbeitsgang mit verhältnismäßig geringem Aufwand hergestellt werden.
Die Wahl des Verarbeitungsverfahrens richtet sich nach der Stückzahl und der Größe der herzustellenden Teile sowie nach den Anforderungen in Bezug auf mechanische Festigkeit und sonstige Eigenschaften, wie z.B. Transparenz, Beschaffenheit der Oberfläche, Maßhaltigkeit usw.
Generell gilt: Der Faserverbundwerkstoff entsteht erst durch das Zusammenfügen von Harz und Fasern, d.h. der Verarbeiter stellt ihn selbst her. Für die Eigenschaften des Endprodukts sind daher ein sorgfältiges Verarbeiten und Aushärten neben der Bauteilauslegung (Faserorientierung, Faseranteil, Lagenzahl und Gewebe) zwangsläufig von entscheidender Bedeutung.
Handlaminat aus Epoxidharz + Glasgewebe (Corvette-Motorhaube)
Festigkeit
Die Festigkeit eines FVW wird wesentlich durch die Verstärkungsfaser bestimmt.
Prinzip 1: Ein Werkstoff in Faserform hat eine vielfach größere Festigkeit als das gleiche Material in anderer Form. Zudem gilt: je dünner die Faser, umso größer ist die Festigkeit. (A.A. Griffith)
Prinzip 2: Ein Verbundwerkstoff kann als Ganzes Spannungen aufnehmen, die die schwächere Komponente zerbrechen würden, während von der stärkeren Komponente im Verbund ein höherer Anteil seiner theoretischen Festigkeit übernommen werden kann, als wenn sie alleine belastet würde. (G. Slayter)
Bei der Betrachtung der Festigkeiten unterscheidet man zwischen statischer und dynamischer Festigkeit.
Die statische Festigkeit bezieht sich auf einfache Belastungsfälle (Zug, Druck, Biegung etc.) während die dynamische Festigkeit das Verhalten bei häufig wechselnder Belastung (Biegewechsel mit wechselnder Kraft und Frequenz, entsprechend kombiniert auftretende Zug-, Druck- und Schubkräfte) bestimmt.
Vor allem dort, wo häufige Biegewechsel auftreten, ist eine gute dynamische Festigkeit erforderlich (z.B. Holmkonstruktionen im Flugzeugbau).
Epoxidharze zeigen selbst bei mehreren zehntausend Lastwechseln den geringsten Festigkeitsabfall und damit die größte dynamische Festigkeit.
Matrix (Harz-Einbettung)
Das Reaktionsharz als Bindemittel (Matrix) hat die Aufgabe, die Fasern zu stützen und die auf das Formteil einwirkenden Kräfte auf sie zu verteilen. Dies macht eine gute Haftung des Harzes auf den Fasern notwendig.
Das Reaktionsharz bestimmt im wesentlichen folgende Eigenschaften: Chemikalienfestigkeit, Alterungsbeständigkeit, Kratzfestigkeit, elektrische Eigenschaften sowie den Schwund beim Härten.
Dichte, Wärmeleitfähigkeit, Wärmedehnung und spezifische Wärme hängen ab vom Mengenverhältnis der Komponenten Reaktionsharz, Reaktionsmittel, Fasern und Füllstoffe.
Fasern
Die mechanischen Eigenschaften der Formstoffe, z.B. Zug-, Biegefestigkeit und Schlagzähigkeit sowie die Fähigkeit zur Arbeitsaufnahme, sind hauptsächlich durch die Eigenschaften der Fasern bedingt. Sie können durch Wahl der Fasererzeugnisse, den Fasergehalt und die Orientierung der Fasern beeinflußt werden.
Härten
Die Eigenschaften des gehärteten Reaktionsharzformstoffes und damit des Formteiles hängen nicht nur vom Ausgangsmaterial ab, sondern auch in hohem Maße von der Führung des Härtungsprozesses. Kenntnisse über die Vorgänge beim Härten des Reaktionsharzes sind daher für den Verarbeiter unerläßlich.
Beim Härten, d.h. beim Übergang der flüssigen Reaktionsharzmassen in dreidimensional vernetzte Produkte, wird zwischen drei Reaktionsarten unterschieden:
Polymerisation (z.B. ungesättigte Polyesterharze)
Unter dem Einfluß von Reaktionsmitteln, z.B. Peroxiden und Beschleunigern, reagieren die Doppelbindungen der Ausgangskomponenten unter Freiwerden von Reaktionswärme miteinander; es entstehen durch Vernetzen der Moleküle der Ausgangskomponenten hochmolekulare Substanzen.
Liegen mehrere Ausgangskomponenten vor, wie z.B. ungesättigte Polyester und Styrol bei UP-Harzen, so spricht man von Mischpolymerisation.
Die Polymerisationsreaktion benötigt nach dem Zugeben der Reaktionsmittel eine gewisse Anlaufzeit. Anschließend geht die Reaktionsharzmasse ohne Freiwerden flüchtiger Produkte verhältnismäßig schnell unter Erwärmung und raschem Ansteigen der Viskosität in den festen Zustand über. Der einmal eingeleitete Härtungsvorgang kann nicht mehr unterbrochen werden und ist irreversibel.
Polymerisations-Reaktion
Polyaddition (z.B. Epoxid-Harze)
Im Gegensatz zur Polymerisationsreaktion werden hier dem Reaktionsharz wesentlich größere Mengen an Reaktionsmitteln zugegeben, und zwar in stöchiometrischen Mengen. Die Eigenschaften des Endproduktes hängen daher sowohl vom eingesetzten Reaktionsharz als auch vom Reaktionsmittel ab. Der Übergang vom flüssigen in den festen Zustand vollzieht sich bei der Polyaddition im allgemeinen langsamer und gleichmäßiger als bei der Polymerisation. Bei der Reaktion wird Wärme frei.
Polykondensation (z.B. Phenolformaldehyd-Harze)
Im Gegensatz zur Polymerisation und Polyaddition reagieren hier die Ausgangskomponenten unter Abspalten von Nebenprodukten, z.B. Wasser. Die Reaktion kann stufenweise durchgeführt werden. Im Allgemeinen werden vorkondensierte Harze verarbeitet, zu deren Härtung meist nur noch Wärme notwendig ist.
Bruchdehnung
Bei einer Zugbeanspruchung darf das Harz nicht vor der Faser brechen, da es sonst durch Risse zu einem Versagen des gesamten Bauteils kommt. Die Bruchdehnung der Harze sollte daher vorzugsweise größer sein, als die der üblichen Verstärkungsfasern.
Harz/Faser-Haftung
Die Güte eines Verbundwerkstoffes hängt vor allem auch von der Haftung des Harzes auf den Verstärkungsfasern ab. Je besser diese Haftung, umso höher ist die Festigkeit.
Um dies zu erreichen, werden Glasgewebe mit Haftvermittlern (Silanen, verschiedenen Finishs) behandelt, damit eine möglichst feste (chemische) Verbindung mit dem Harz entsteht. Eine Ausnahme bilden Aramidfasern (Kevlar®, Twaron®) für die kein chemischer Haftvermittler verfügbar ist. Kohlenstofffasern werden mit einer Epoxidharzschlichte versehen.
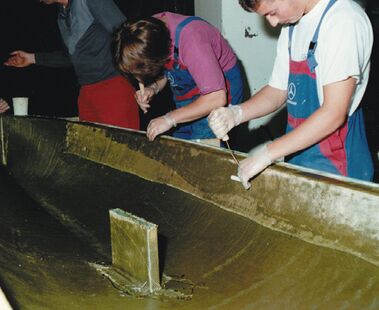
Handlaminat
Tränken eines Kohle/Aramid-Gewebes mit Epoxidharz
für einen Segelflugzeugrumpf
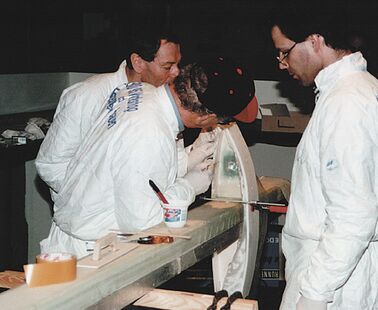
Handlaminat
Verkleben von Tragflächenrippen auf einen Holm aus GFK
(Flugzeugbau-Workshop der Aero-Luftfahrtmesse, Friedrichshafen).
(Nach VDI-Richtlinie 2010 und Ehrenstein, Faserverbundkunststoffe, Hanser-Verlag)
Einsatzgebiete von Faserverbundwerkstoffen und die besonderen Eigenschaften
Bildnachweis
Raumfahrt: NASA; Luftfahrt: Hexion AG (Bakelite); Sport- und Freizeit: Oxeon; Fahrzeugbau/Verkehrstechnik: O.C.P. Kunststoffe Lyss via Swiss-Composite; Maschinen- und Anlagenbau: Wacker-Chemie; Medizintechnik: Die Wethje bzw. Hexion/Bakelite